The BUSS-Loop® Reactor is, since its origin, the icon and the benchmark for superior efficiency in reaction technology.
This is due to its elegent design and instrinsic ability to cope with the challenges of reaction engineering, like mass transfer, mixing, heat transfer, catalyst handling, flow chemistry, safety and process intensification towards sustainability.
The Buss Loop® reactor basic concept is a system consisting of a reaction autoclave, a circulation pump, a heat exchanger and a reaction mixer (high-performance gas/liquid ejector), designed to achieve high mass transfer rates and homogeneous mixing while safely ensuring the necessary heat duty for the chemical reaction.
These key features result in precious benefits:
-
shorter reaction times
-
catalyst saving
-
optimized reaction volume and productivity
-
constant quality
-
flexibility both for single product and multipurpose plants
-
linear scale-up
-
tailored heat exchange
-
operability of the headspace gas phase
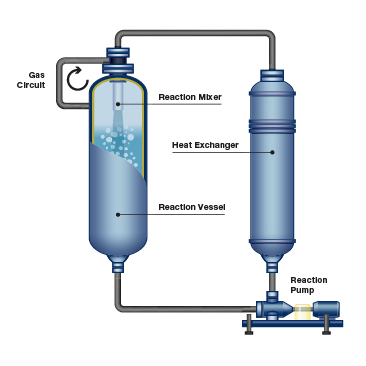
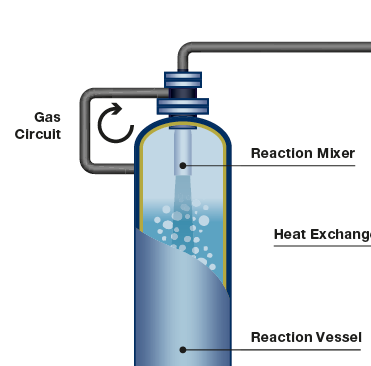
Highest Mass Transfer
The BUSS-Loop® Reactor is known to be the industrial reactor choice in practice yielding the highest specific mass transfer performance.
The reaction mixer is in fact a high-performance gassing tool. The reaction pump circulates fluid through a nozzle, which increases the velocity and pressure on the outlet side – the so-called “Venturi effect”. This effect is used in two ways by a BUSS-Loop® Reactor. First, the high-speed jet entrains a large amount of gas as it enters the reaction vessel. Second, the vacuum it creates, is used to draw gas from the reactor headspace back into the jet mixer.
This twin action results in the formation of extremely small gas bubbles that are dispersed into the liquid phase thus achieving a very intimate mixing of the gas and liquid phases which in turn, promotes very high mass transfer rates.
The ability to generate and finely disperse very small gas bubbles, makes this an ideal tool as a primary dispersion device for gas-liquid reactors. The two-phase mixture created in the reaction mixer is then injected into the fluid of the reaction vessel, where the homogenous mixing ensures that the catalyst, if present both as heterogeneous and homogeneous form, can perform with maximum activity.
Homogeneous Mixing
The BUSS-Loop® Reactor provides intensive mixing due to the high dissipation of enery in the venturi-style jet ejector “shock zone” and the high velocity impingement in the reaction vessel.
In addition, the impingement of the high velocity flow in the reaction vessel causes intensive secondary (bulk) mixing.
The absence of baffles or any heat exchange devices in the reaction vessel, combined with the high turbulence and velocity, ensure homogeneous mixing and back mixing, with patterns that are scalable from laboratory- and pilot plant-scale to industrial-scale units.
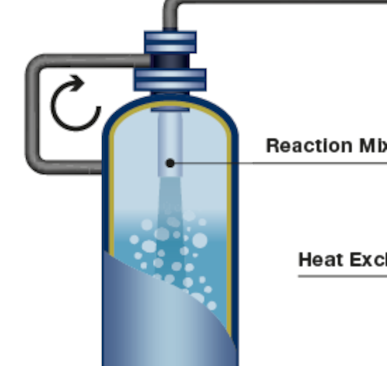
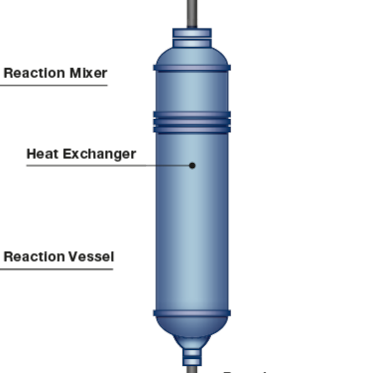
Efficient Heat Transfer
The BUSS-Loop® Reactor, instead of coils or internal exchangers, benefits from an external heat exchanger that can be built as large (or as small) as required by the reaction duty and is not limited by the reactor’s working volume.
The full heat exchanger area is available, even if the reactor is operated with reduced working volumes, for example in semi-batch operation.
This creates a great advantage in dealing with the peaks of heat duty of highly-exotermic reactions, or reducing the heat-up time of the reactor charge, with proper design of the secondary circuit as needed.
The external heat exchanger, combined with the high velocity of the reaction volume circulation, allows to maintain a very homogeneous temperature profile of the entire reaction volume, resulting in excellent quality control and consistent performance.
Contact Us
* Required fields
Your Contact
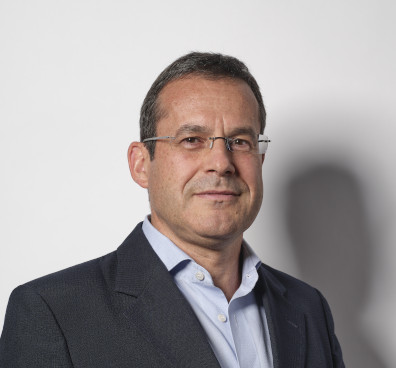
Gianluca Premolil
Business Manager Reaction Technology
Other topics of interest
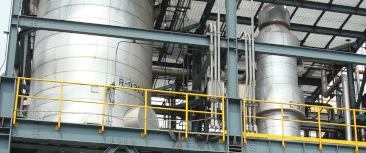
Continuous Operation with the BUSS-Loop®
The BUSS-Loop® Reactor can operated be designed for continuous as well as batch and semi-batch operation.
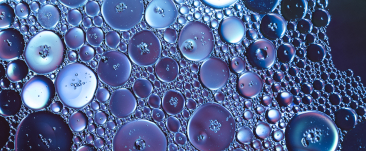
Our Chemical Reaction Experience
Click below to discover the myriad reactions we have experience with, through experiments in lab- and pilot-scale and/or full-scale plant design.
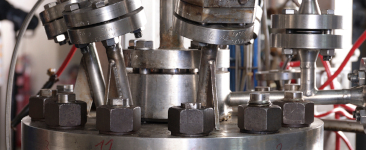
PRocess Development Capabilities
Every plant comes with guarantees. The basis of the guarantees, as well as the process design itself, is developed in our own extensive technical center.