Plastics are one of the most useful classes of material ever invented. For many of its applications, doing without plastic is almost unthinkable. However, plastic’s durability is also a disadvantage once it “leaks” out to the environment. So what do we do? We need to rethink living with plastics.
The demand for plastics is expected to increase significantly despite growing public demand that we use plastics more efficiently and handle waste plastic more effectively.
Strategies to deal with these issues vary in the details, but a consensus on the high-level approach to the problem is forming. That approach is often described by a very brief phrase. In order or priority it is “Reduce, Reuse, and Recycle”.
After making an honest assessment of global trends of human behavior, it is clear that reducing and reusing plastics will not, by themselves, solve the problem. Even if we stopped all production immediately, and re-use what we could, there would still be literal mountains of plastic waste all around the world.
So “Recycle” must play a role. There are many methods of recycling: mechanical, physical, chemical, and others. And here, it must be recognized that there is an important criteria in setting the heirarchy of the methods. Namely, the method that impacts the environment the least, should have highest priority and so on.
Employing this criteria leaves chemical recycling at, or at least very near, the bottom. Why? It takes more energy than most of the other methods to convert the plastic waste into useable materials to manufacture new products.
After all this, there is still a critical role for chemical recycling to play. There are many materials that are not able to be recycled by other methods or for applications where these other methods cannot provide the product quality and/or characteristics they require.
This is where pyrolysis, one type of chemical recycling and the basis of our technology, shines.
OUR CHEMICAL RECYCLING TECHNOLOGY INCLUDES:
Pre-Treatment & Material Handling
Some raw materials may require treatment for chemical recycling. The raw material should be delivered to the chemical recycling plant shredded, dried, metal- and inorganic fiber-free.
If you need assistance with the mechanical process steps and/or with a conveying system to deliver the raw material from the source to the chemical recycling plant, let us know. Using our partners, we can provide a one-stop solution.
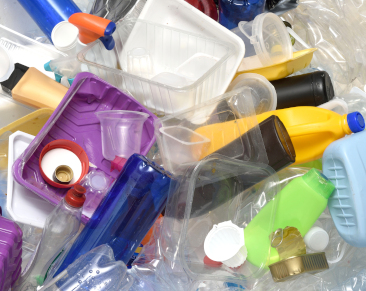
Feeding/extrusion
Once the raw material is conveyed to the chemical recycling plant, it is fed to pre-heat and extrusion equipment.
This critical step delivers a continuous supply of raw material in a the proper semi-molten state to the pyrolysis reactor and helps ensure the reactor will run at its highest efficiency.
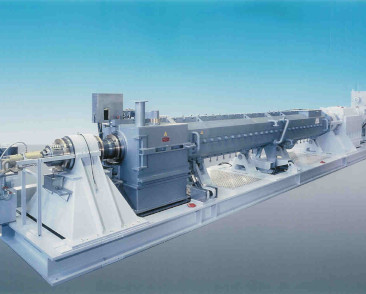
Flash Pyrolysis
The patented Flash Pyrolysis Reactor is the heart of the BUSS ChemTech Chemical Recycling Plant.
It delivers just the right amount of heat to the semi-molten mixed waste plastic to obtain the desired high quality products while minimizing losses (in the form of by-products) and energy use.
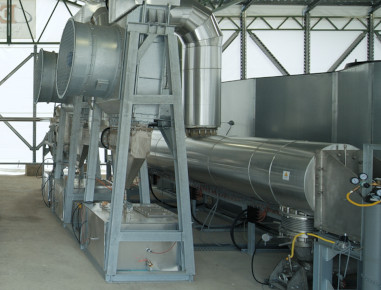
Oil Fractionation & Post-Treatment
Each customers’ needs are different. (We are not telling anything you don’t know!)
Whether ensuring the highest yield of pyrolysis only – regardless of chain length – or several cuts of various chain length ranges are required, we can tailor the oil fractionation to obtain the desired products.
In addition, we have the hydrogenation expertise, and with our partners other purification techniques, to modify the products to make them cracker ready.
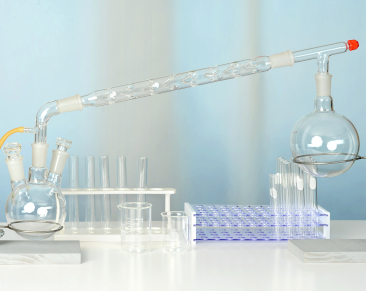
Solids Removal
Raw materials with “typical” properties, will generate roughly 5 wt-% high carbon content solid by-product.
The removal of the solids is a patented feature of our chemical recycling technology. Proper removal is critical for achieving high quality pyrolysis oil. Without one, you don’t have the other.
Normally, letting the solids drop into barrels is sufficient, but if a close system is required due to local regulations, we can supply this equipment as well.
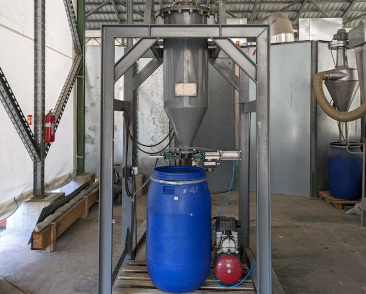
Gas Treatment
Our Flash Pyrolysis Reactor delivers combustible gases that can be directly used (see Energy Recovery below) or stored for eventual sale.
Some raw materials may contain environmentally unfriendly compounds that end up leaving the Flash Pyrolysis Reactor in the gaseous phase. For these instances, we supply absorption equipment to remove and/or neutralize these compounds before the gas is used for energy.
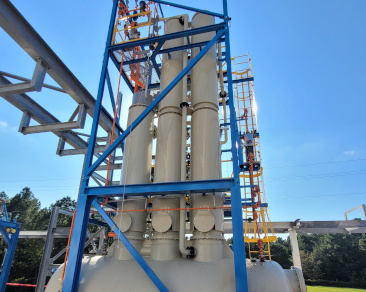
Energy Recovery
A key feature of our Chemical Recycling Technology is that it is energy neutral.
Utilizing a gas engine within the chemical recycling process allows the plant to supply itself – and much of any ancillary equipment required – with electrical energy.
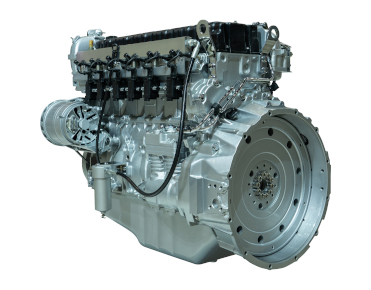
OUR CHEMICAL RECYCLING TECHNOLOGY INCLUDES:
Pre-Treatment & Material Handling
Some raw materials may require treatment for chemical recycling. The raw material should be delivered to the chemical recycling plant shredded, dried, metal- and inorganic fiber-free.
If you need assistance with the mechanical process steps and/or with a conveying system to deliver the raw material from the source to the chemical recycling plant, let us know. Using our partners, we can provide a one-stop solution.
Feeding/extrusion
Once the raw material is conveyed to the chemical recycling plant, it is fed to pre-heat and extrusion equipment.
This critical step delivers a continuous supply of raw material in a the proper semi-molten state to the pyrolysis reactor and helps ensure the reactor will run at its highest efficiency.
Flash Pyrolysis
The patented Flash Pyrolysis Reactor is the heart of the BUSS ChemTech Chemical Recycling Plant.
It delivers just the right amount of heat to the semi-molten mixed waste plastic to obtain the desired high quality products while minimizing losses (in the form of by-products) and energy use.
Oil Fractionation & Post-Treatment
Each customers’ needs are different. (We are not telling anything you don’t know!)
Whether ensuring the highest yield of pyrolysis only – regardless of chain length – or several cuts of various chain length ranges are required, we can tailor the oil fractionation to obtain the desired products.
In addition, we have the hydrogenation expertise, and with our partners other purification techniques, to modify the products to make them cracker ready.
Solids Removal
Raw materials with “typical” properties, will generate roughly 5 wt-% high carbon content solid by-product.
The removal of the solids is a patented feature of our chemical recycling technology. Proper removal is critical for achieving high quality pyrolysis oil. Without one, you don’t have the other.
Normally, letting the solids drop into barrels is sufficient, but if a close system is required due to local regulations, we can supply this equipment as well.
Gas Treatment
Our Flash Pyrolysis Reactor delivers combustible gases that can be directly used (see Energy Recovery below) or stored for eventual sale.
Some raw materials may contain environmentally unfriendly compounds that end up leaving the Flash Pyrolysis Reactor in the gaseous phase. For these instances, we supply absorption equipment to remove and/or neutralize these compounds before the gas is used for energy.
Energy Recovery
A key feature of our Chemical Recycling Technology is that it is energy neutral.
Utilizing a gas engine within the chemical recycling process allows the plant to supply itself – and much of any ancillary equipment required – with electrical energy.
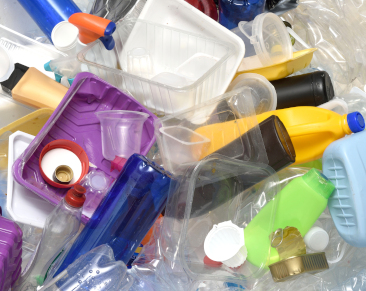
Raw Materials
It is true, the “purer” and the “cleaner” a waste plastic stream is, the higher the yield of desirable product and the lower the operating costs – of the chemical recycling plant. However, it also takes effort (in terms of equipment and energy) to separate polymer types and to ensure a minimum of impurities.
In some instances, it may be more environmentally friendly and economically sound to process the “mixed” and “dirty” stream with a process that is designed to handle it. This is where BUSS ChemTechs novel chemical recycling technology comes in. We can handle mixed plastic waste with the following properties:
- Polymer types: PE, PP, PA, PS, PC, ABS
- Paper, textiles, wood: max. 5-7%
- PVC: up to 3%
- Organics: max. 7-10%
- Moisture: max. 7-10%
Contact Us
* Required fields
Your Contact
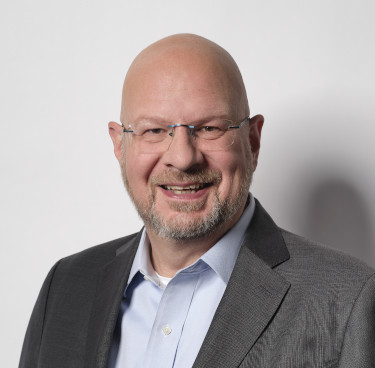
Thomas Blocher
Business Manager Chemical Recycling
Other Topics of Interest
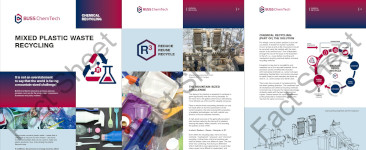
Fact Sheet:
Chemical Recycling
To learn more about our view of chemical recycling’s role, and pyrolysis in particular, as well a bit more about our technology, click below.
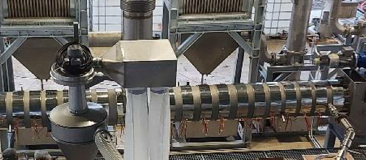
Our Scope of Supply
From technology packages to modular and turnkey solutions, click below to find out about our range of services.

Team & Skills
We have the relevant resources to deliver useful engineering documents, robust equipment and experienced personnel for your project. Click more to learn.