We rapidly scale your process from the lab to industrial production.
In our methodology for scaling up processes, we start with fundamental feasibility experiments and the determination and optimization of key process parameters, typically executed on a laboratory scale.
For scale-up trials, we utilize our pilot loop reactors, which have volumes ranging from 15 to 50 liters. Scaling is often associated with challenges, as not all processes can simply be scaled linearly. Differences in reactor geometry, thermodynamic properties and material behavior must be taken into account.
The scale-up of processes in the loop reactor is highly reliable and can be achieved with a scale-up factor of up to 4000 in a single step. Furthermore, the results of these scale-up trials form the basis for providing performance and process guarantees to our clients. This ensures that we not only deliver effective and efficient scale-up solutions but also offer the confidence and assurance our clients need for their industrial applications
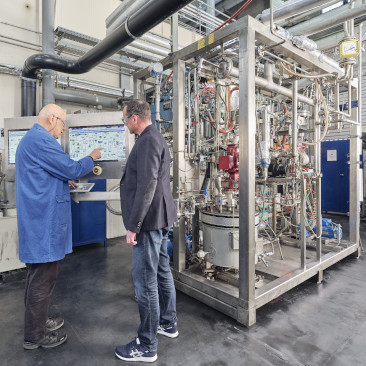
The SRM-15
Our 15 Liter BUSS-Loop® Reactor is our work horse. This pilot unit is suitable for batch and continuous reactions as well as for corrosive reactions materials.
- 15 liter working volume
- 50 barg maximum operating pressure
- 220°C maximum operating temperature
- Hastelloy C-200 wetted parts
The SR-50
Our 50 Liter BUSS-Loop® Reactor is our largest unit and is designed for higher pressure applications that are only moderately corrosive. In addition, it can be equipped with the style of “jet ejector” used for alkxoylation reactions
- 50 liter working volume
- 100 barg maximum operating pressure
- 275°C maximum operating temperature
- 1.4571 wetted parts (316ss)
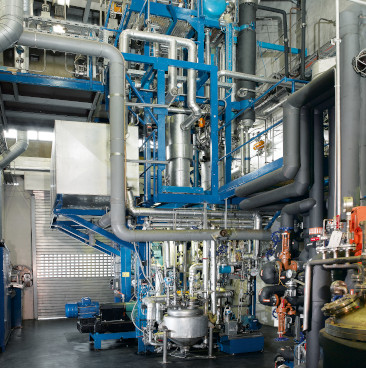
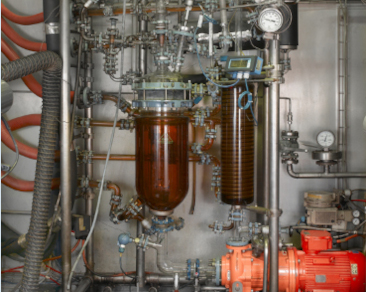
The APR-15
Our 15 Liter Advanced Phosgenation Reactor is installed in a closed and purged containment which allows us to run highly toxic reactions like phosgenation.
- 15 liter working volume
- 0.5 barg maximum working pressure
- -20°C to 180°C operating temperature range
- Glass and PTFE wetted parts
The Pyrolysis Unit
The newest unit in our family pilot plants is a 100 kg/h pyrolysis reactor based on our patented mixed plastic waste recycling technology.
This unit is used to test and characterize the mixed waste plastic stream that will be the raw material for the full-scale facility. In addition, we determine the end-product specifications and full-scale plant throughput.
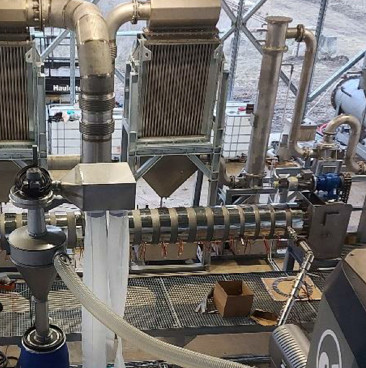
Success Stories
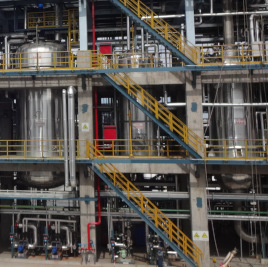
BUSS ChemTech delivers first integrated HCR/HHCR plant
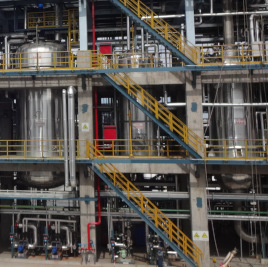
Based only on lab-scale tests to characterize the client’s raw material, we delivered a Technology Package for an integrated polymerization and hydrogenation plant to produce base and water white hydrocarbon resins.
Learn More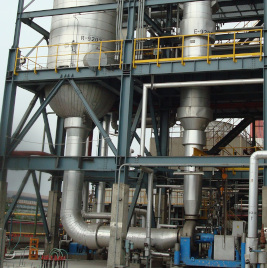
Development of a continuous SBS hydrogenation process
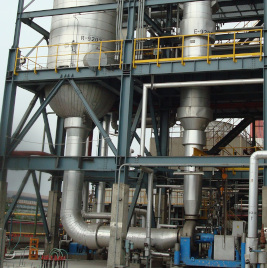
Demonstration of feasibility, first on a lab-scale (batch), then on the pilot-scale (continuous). Subsequent contract for the industrial plant.
Learn MoreContact us
* Required fields
Other Topics of Interest
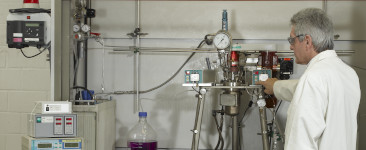
Let us evaluate
your chemistry
From literature search to conducting experiments to determine the economic feasibility of your chemistry, we are a reliable development partner.
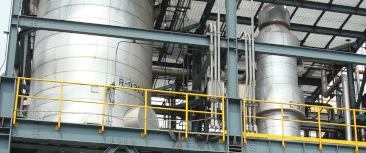
Designing Commercial Scale Plants
Taking results from lab and pilot-scale experiments and designing an industrial plant is something we do every day. Check out our Fact Sheet.
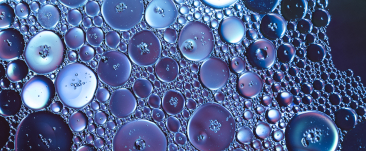
Our Chemical Reactions Experise
Our experience encompasses literally hundreds of reactions of all types. A sampling of these reactions can be found by clicking the link below.