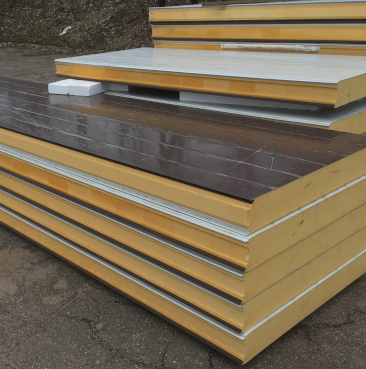
Aniline
Aniline is the precursor of methylene diphenyl diisocyanate (MDI) and it can be obatined by the catalytic hydrogenation of (mono) nitrobenzene.
With the BUSS-Loop® Reactor, the process can be carried out in the slurry phase with a heterogeneous catalyst. Furthermore, it can be run in continuos operation mode thanks to our development of an inline filtration system (located directly in the “loop”) and an ingenious catalyst inventory management system.
Toluenediamine
Toluenediamine (TDA) is the precursor of toluene diisocyanate (TDI) and is obtained by hydrogenation of dinitrobenzene (DNB).
The suitability of the BUSS-Loop® Reactor Technology for TDA production was proven decades ago as reported by Dow Chemical’s Mr. Renato Paludetto by ICP Rivista DeII’ Industria Chimica anno XXXIII-No.1 Gennaio 2005 in the proceedings of the Chemical Day 2004, pp. 28-30.
Mr. Paludetto’s presentation “Improved Process for the hydrogenation of Dinitrotoluene (DNT) to Toluenediamine (TDA)” came to be as the result of a successful partnership. In fact, in 1999 a partnership was formed between EniChem (whose polyurethane business was acquired by Dow in 2001) and BUSS ChemTech (at the time named Kvaerner Process Technology) to develop an alternative and improved technology for the hydrogenation of DNT to TDA. The specific goals of the development were reducing catalyst costs (active metals, mechanical losses), improving process selectivity by reducing heavy by-products, and reducing overall investment costs.
The collaboration proceeded through all phases of process development, from chemistry evaluation and optimization, to pilot-scale verification of the scale-up parameters, all while achieving the named goals. One remarkable aspect was the design of a continuous process, including the development of an inline filtration system within the circulation loop.
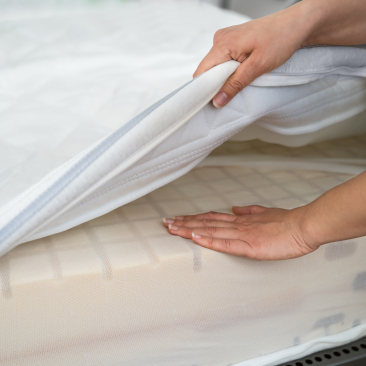
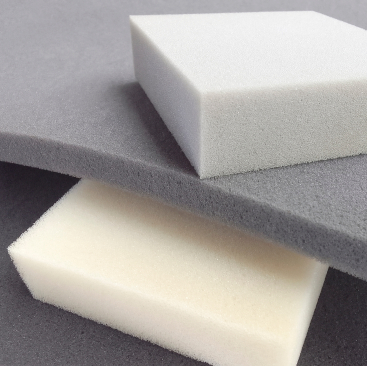
Isocyanates
Isocyanates like methylene diphenyl diisocyanate (MDI) and toluene diisocyanate (TDI) are respectively produced by the phosgenation of Aniline and Toluendiamine (TDA).
With its expertise in handling phosgene and phosgenation reactions, BUSS ChemTech is uniquely positioned to support the process development of this important step in the production chain.
Polyether Polyols
Polyether polyols are obtained by the alkoxylation of poly-alcohol chain starters and alkene oxides. The reaction is catalysed by metal hydroxides or double-metal cyanides (DMC), these latter providing higher kinetics and narrower molecular weight distributions.
Polyether polyols are mainly used in the production of polyurethane foams (rigid or flexible type) and CASE (coating, adhesive, sealant, and elastomer) applications. Chemically, they are characterized by hydroxyl groups that, further reacting with isocyanate groups, confer to the resulting polyurethanes the desired mechanical properties.
According to the final application, polyether polyols can be produced in a large variety of molecular weights. BUSS ChemTech can support its customers in the configuration of the optimized plant configuration and in the design of the relevant product recipes, according to the requested characteristics of the final product.
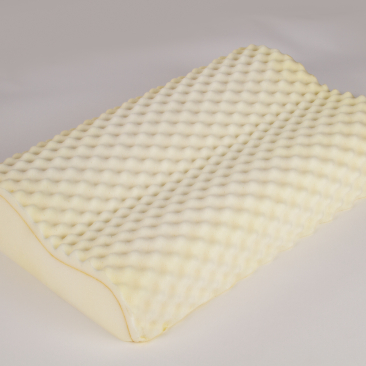
Contact Us
* Required fields
Your Contact
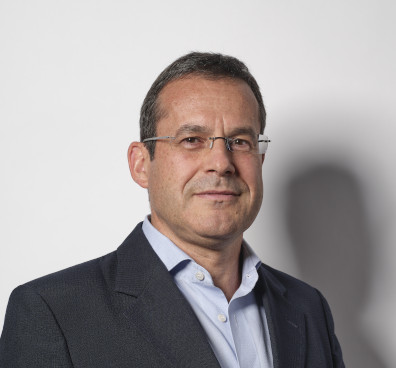
Gianluca Premoli
Business Manager Reaction Technology
Other Topics of Interest
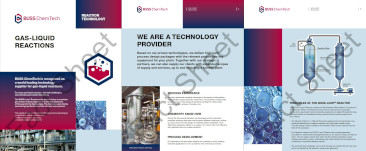
Fact Sheet:
Gas-Liquid Reactions
Hydrogenation is an important reaction in many of the production steps for polyurethane. Learn more about we can assist you in our Fact Sheet.
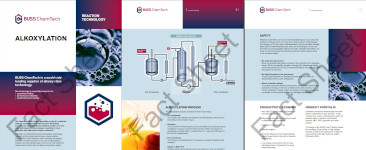
Fact Sheet:
Alkoxylation
Producing polyols or thinking about producing them? Read about our technologyies including continuous reactions with DMC catalysts.
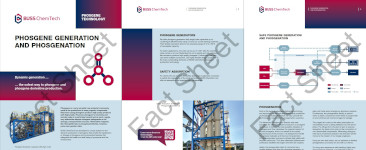
Fact Sheet:
Phosgene Chemistry
Many isocynates are made with phosgenation reactions. Learn about our phosgene and phosgentation technology in our Fact Sheet.