
Development of a continuous SBS hydrogenation process
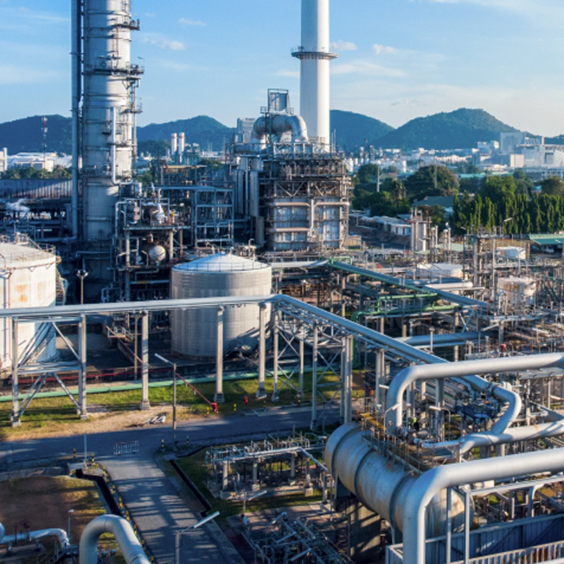
Client
Asia
Plant Capacity
30,000 mtpy Styrene-Ethylene-Butylene-Styrene (SEBS)
Start-up
2010
Scope of work
Development Services, Basic Engineering and Key Equipment Package for a continuous SEBS plant
Project Description
Demonstration of feasibility, first on a lab-scale (batch), then on the pilot-scale (continuous). Subsequent contract for the industrial plant.
Key features
In-situ generation of the active hydrogenation catalyst, scale-up factor of 1:3000, the largest continuous BUSS-Loop® Reactor built by BUSS ChemTech.
Styrene-ethylene-butylene-styrene (SEBS) is an important thermoplastic elastomer (TPE). It is produced by hydrogenating styrene-butadiene-styrene copolymer (SBS), which improves its thermal stability and weather resistance. SEBS behaves like rubber without the need for vulcanization. Thanks to its excellent physical properties, the elastomer has a wide range of applications, e.g. in medical products, in the automotive industry and in household appliances.
The client approached BUSS ChemTech in 2005 to discuss their desire to build a new plant for the continuous production of SEBS. In 2006, we conducted experiments to determine the feasibility of the reaction in batch mode. A 500-ml reactor simulating BUSS-Loop® conditions was used. After successfully demonstrating the viability of the concept, the client invested in further tests to determine feasibility of running the reaction in a continuous mode. These tests were conducted in a 15-liter BUSS-Loop® Reactor.
The tests were successful, so a last set of experiments were ordered by the client to optimize the continuous reaction, including the in-situ production of the catalyst. After evaluating the CAPEX and OPEX of the new plant as proposed by BUSS ChemTech, the client approved the investment. The industrial plant started up in 2010. The client was so pleased with its performance, that they ordered a 2nd plant in 2012.
The client approached BUSS ChemTech in 2005 to discuss their desire to build a new plant for the continuous production of SEBS. In 2006, we conducted experiments to determine the feasibility of the reaction in batch mode. A 500-ml reactor simulating BUSS-Loop® conditions was used. After successfully demonstrating the viability of the concept, the client invested in further tests to determine feasibility of running the reaction in a continuous mode. These tests were conducted in a 15-liter BUSS-Loop® Reactor.
The tests were successful, so a last set of experiments were ordered by the client to optimize the continuous reaction, including the in-situ production of the catalyst. After evaluating the CAPEX and OPEX of the new plant as proposed by BUSS ChemTech, the client approved the investment. The industrial plant started up in 2010. The client was so pleased with its performance, that they ordered a 2nd plant in 2012.
Contact us
* Required fields